Выбор параметров лазера для качественной резки
Оригинал статьи вы можете найти на сайте ntoire-polus.ru
Скорость резки металла определяет производительность лазерных технологических установок, при этом существенным параметром является величина шероховатости боковой стенки реза Rz. Лазерная резка позволяет получать готовые детали без последующей финишной обработки, и альбом технологий промышленных лазерных станков на основе СО2-лазеров содержит условия качественной резки для широкого набора материалов. Для технологических волоконных лазеров подобный альбом пока только формируется, и технологи производств сталкиваются с проблемами выбора параметров волоконных лазеров, наиболее подходящих для задач конкретного производства.
В литературе подробно рассматривались различные факторы, которые могут оказать влияние на качество газолазерного реза и на глубину проплавления металла при лазерной сварке. К ним относят (см. обзор [1]): микронеустойчивости (термокапиллярную, Рэлей-Тейлоровскую, капиллярно-испарительную, капиллярно-ветровую), образование «ступеньки» на фронте проплава и реза, неустойчивость пленочного погранслойного течения расплава и др. Отметим, что многие авторы считают нужным упомянуть о большой сложности процессов внутри лазерного реза и о возникающих из-за этого затруднениях при попытках однозначно интерпретировать экспериментальные результаты.
На рис.1 показана боковая поверхность реза малоуглеродистой стали толщиной 5 мм, выполненного с помощью волоконного лазера ЛС-3.5 производства НТО «ИРЭ-Полюс». Лазер снабжен транспортным волокном с диаметром сердцевины 100 мкм и характеризуется параметром качества выходного пучка M2 = 13,5. Рез получен с использованием оптической головки фирмы OPTOSKAND. В данной головке установлена коллимирующая линза с fc = 120 мм и фокусирующая линза с ff = 200 мм. Соответствующее фокальное пятно имело диаметр d = 190 мкм, глубина фокуса ZR = 2 мм. Мощность лазера составляла 3,5 кВт, режущим газом являлся воздух. Резка производилась на скорости 3 м/мин.
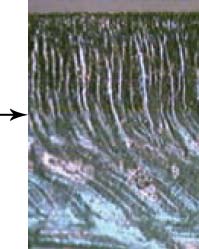
Рис. 1 - Боковая поверхность реза малоуглеродистой стали
Стрелкой отмечена глубина, ниже которой характер реза существенно изменялся. Подобные картины резов наблюдаются и при использовании СО2-лазеров.
Можно предположить, что на соответствующей глубине прекращается эффективное канализирование пучка лазера внутри реза, пучок рассеивается на большие углы и поглощается боковыми стенками. Материал ниже стрелки прогревается и плавится не за счет прямого воздействия лазерного излучения, а в основном за счет раскаленной газовой струи и теплопроводности металла. Рассеяние может происходить на сравнимых с длиной волны лазера неоднородностях, возникающих из-за упомянутых выше микронеустойчивостей, которые имеют весьма большие инкременты развития.
Поскольку лазерные пучки, в том числе и многомодовые, всегда частично когерентны, старт к развитию неоднородностей может дать интерференция между центральной частью пучка и его периферией, отражающейся от стенок реза. Интерференция вызывает пространственную модуляцию интенсивности излучения внутри реза и соответствующую неоднородность воздействия излучения на материал.
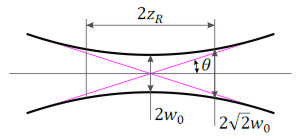
Рис. 2 - Продольное сечение осесимметричного лазерного пучка
Рассмотрим данную интерференцию в простой модели. Используем принятое обобщенное описание лазерных пучков.
На рис. 2 приведено продольное сечение осесимметричного лазерного пучка, распространяющегося вдоль оси z и имеющего перетяжку в точке z=0. Границей лазерного пучка (по уровню интенсивности 1/e2) является гиперболоид вращения, угол θ определяет расходимость пучка в дальней зоне. Зависимости радиуса лазерного пучка w и радиуса кривизны его волнового фронта R от z описываются следующими формулами:
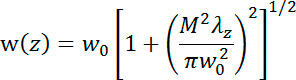
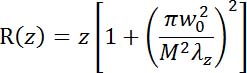
Здесь λ — длина волны излучения, безразмерный параметр M2 ≥ 1 характеризует отклонение лазерного пучка от идеального гауссова (для последнего M2=1) и определяет «фокусируемость» лазерного луча, то есть радиус w0 в перетяжке (точном фокусе объектива) в соответствии с формулой
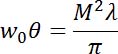
Глубину фокуса или, как его часто называют, длину перетяжки, то есть длину, на которой диаметр пучка меняется в √2 раз, удобно характеризовать так называемой рэлеевской длиной zR (см. рис. 2):
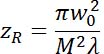
Длина перетяжки равна удвоенной величине zR. На рис.3 схематично представлено распространение лазерного пучка внутри реза. Максимальная толщина металла, для которой возможен «чистый» рез, обозначена как x0. Перетяжка режущего излучения расположена на поверхности материала.
В результате эксперимента хорошо известно, что ширина реза в таком случае примерно совпадает с диаметром перетяжки. Распространение луча обозначено «отражением» гиперболических асимптот от боковых стенок реза.
kλ — разность хода между периферической и центральной частями луча (достигаемая на выходе реза), при которой возникающие из-за интерференции неоднородности еще не приводят к рассеянию на большие углы и возможен «чистый» рез материала толщиной x0.
Поскольку kλ = x0Θ2, из формул (3), (4) легко получить следующее выражение:
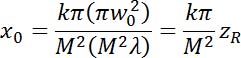
Таким образом, в предположении интерференционной природы эффектов, приводящих к ограничению глубины проникновения излучения внутрь реза, предельная глубина «чистого» реза пропорциональна глубине фокуса и обратно пропорциональна параметру M2, определяющему исходное качество лазерного пучка.
Входящий в формулу безразмерный коэффициент k попытаемся определить из известных экспериментальных данных.
Из альбома технологий для комплекса «Трумпф» на основе СО2-лазера (λ = 10,6 мкм) с мощностью 3,2 кВт, имеющего на выходе пучок, близкий к идеальному гауссову пучку (M2 = 1,1) с диаметром на фокусирующей линзе 20 мм, при фокусном расстоянии линзы f = 180 мм максимальная толщина малоуглеродистой стали, для которой возможен чистый кислородный рез с одинаковым Rz по всей боковой поверхности, составляет 15 мм. Для этих параметров в фокусе линзы имеем: Ф = 0,056 рад, w0 = 0,067 мм, zR = 1,2 мм. Тогда из выражения (5) получаем k ~ 4,4.
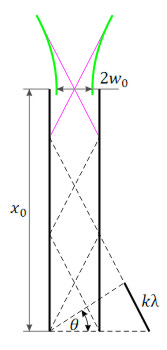
Рис. 3 - Распространение лазерного пучка внутри реза
Для упомянутого выше волоконного лазера ЛС-3.5 с оптической головкой, имеющей фокусные расстояния коллиматора и объектива соответственно fc = 120 мм и ff = 200 мм, при которых параметры в фокусе составляют: Ф = 0,048 рад, w0 = 0,096 мм, zR = 2 мм,— одинаковое по всей высоте значение Rz, соответствующее «чистому» резу, получено для малоуглеродистой стали толщиной до 3 мм. Подставляя эти значения в (5), получаем k ~ 6,5.
Хотя формула (5) носит оценочный характер и не учитывает ряд эффектов, связанных с формированием газовой струи и положением перетяжки относительно поверхности материала, значения коэффициента k, полученные для разных типов лазеров и различающихся в 5 раз толщин обрабатываемого материала, оказались близкими (если взять среднее значение, то отклонение в пределах ±20%).
В целом справедливость выражения (5) подтверждена в известных нам экспериментах на действующих установках с волоконными лазерами в Нижнем Новгороде (2 кВт) и Дубне (1 кВт), где используются лазеры с транспортным волокном 50 мкм (соответствующее значение М2 = 6,5).
Как видно из соотношения (5), при заданной ширине реза, определяемой размером пучка в перетяжке 2w0, глубина фокуса, а следовательно и глубина «чистого» реза обратно пропорциональна длине волны излучения λ, то есть при прочих равных условиях лазер с меньшей длиной волны должен обеспечивать большую глубину «чистого» реза. Но еще сильнее, чем от длины волны, глубина «чистого» реза зависит от оптического качества пучка M2 — при фиксированной ширине реза зависимость обратная квадратичная. С этим связано полученное нами в экспериментах с волоконным лазером существенно меньшее значение «чистого» реза по сравнению с аналогичными данными для одномодового СО2-лазера той же мощности. Для увеличения толщин обрабатываемых материалов необходимо повышать качество лазерных пучков. Так, при использовании волоконного лазера с транспортным волокном с диаметром жилы 50 мкм (M2 = 6,5) вместо 100 мкм (M2 = 13,5) при том же диаметре перетяжки около 0,2 мм максимальная толщина «чистого» реза составит 13 мм. Еще более эффективны в этом отношении одномодовые волоконные лазеры. Правда, в настоящее время коммерчески доступны одномодовые волоконные лазеры с выходной мощностью менее 1 кВт.
Для технологов, применяющих волоконные лазеры, приведем дополнительное полезное соотношение.
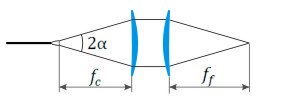
Рис. 4 - Схематичное изображение оптической головки волоконного лазера
На рис. 4 схематически изображена оптическая головка волоконного лазера. На выходе из оптического многомодового транспортного волокна лазерный луч расходится с углом раствора 2α, который для иттербиевых лазеров и волокон с диаметрами 50–300 мкм составляет ~ 0,16 рад. Далее луч преобразуется в плоскопараллельный пучок коллимирующим блоком линз с фокусным расстоянием fc и фокусируется на материал объективом с фокусным ff. Из формул (3)-(5) легко получить следующее выражение для максимальной глубины чистого реза:
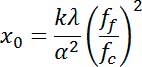
То есть глубина чистого реза определяется только квадратом отношения фокусов линз в оптической головке и не зависит от диаметра используемого транспортного волокна. Размерный коэффициент перед скобками составляет ~ 1 мм. Отметим, что для одномодового лазера и одномодового транспортного волокна 2α=0,1 рад и данный коэффициент ~ 3 мм.
По результатам наших экспериментов можно сделать предварительный вывод об обратной пропорциональности скорости качественного реза толщине материала при прочих равных условиях (при заданных мощности лазера, диаметре транспортного волокна и характеристиках оптической головки).
С другой стороны, скорость реза прямо пропорциональна плотности мощности излучения на материале, то есть при равных характеристиках оптической головки обратно пропорциональна квадрату диаметра транспортного волокна.
Выполненная работа дает расчетную основу для выбора типа и параметров волоконных лазеров, исходя из конкретных условий их применения в технологических системах.
Литература:
- «Анализ моделей динамики глубокого проникновения лазерного излучения в материалы» (Часть 1. Нестационарная гидродинамика в процессах взаимодействия лазерного излучения с веществом. Часть 2. О механизмах удаления расплава при газолазерной резке материалов), проф. В.С. Голубев, — Сборник трудов ИПЛИТ РАН, 2004.