Linear drive
The following diagrams show linear movement according to three most common kinematic schemes of portal mechanism used in modern machinery manufacturing: ball screw, gear rack (rack & pinion) and linear drive (direct drive).
Ball screw unit
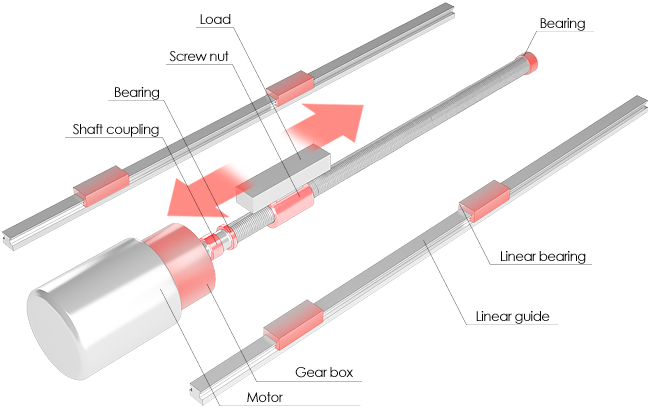
- Components subject to mechanical wear
Gear rack
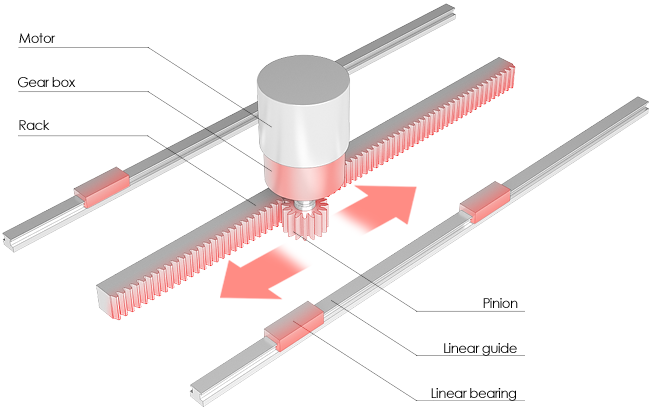
- Components subject to mechanical wear
Linear drive
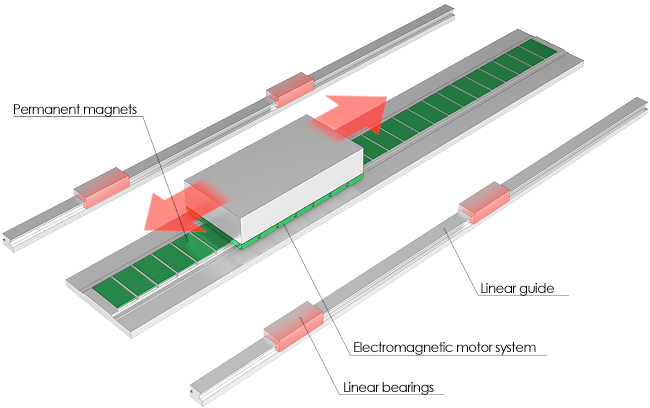
- Components subject to mechanical wear
- Components free from mechanical wear
Comparison between ball screw unit and direct drive
The structure of the ball screw unit possesses the big number of mechanical joints resulting in wear and consequently lower processing accuracy. In its turn, the linear drive consists of just two parts, which interact only at the electromagnetic level. The parts do not contact mechanically and, as a result, the mechanical wear of the linear drive is absent.
It’s worth mentioning that the ball screw systems for long travels show extra problems due to additional mechanical tension having appeared due to screw deflection. Such systems demand precise engineering calculations and high quality components. To sum up, some manufacturers may provide unreliable coordinate systems since they do not possess satisfying engineering facilities.
Comparison of rack & pinion and direct drive features
Unlike the ball screw, the rack & pinion do not show tension and high inertial load to the motor. Nevertheless, it still demands high quality production of the coordinate system: high precision installation of guides, rack & pinion, gear box and motor. Machine bed of decent quality and close fitting let the rack &pinion based on the hardened gear pinion enable long and stabile machine operation.
However, errors and tolerances can result in backlash and fast mechanical wear of the drive. As in the previous case, some manufacturers may provide unreliable coordinate systems since they do not possess satisfying engineering facilities.
Let’s consider the control processes in each case
Ball screw and rack & pinion consist of subject to wear components: a shaft, pulley, screw, balls, nut, etc. Linear drive includes only rotor and stator separated by air space. Since no middle elements are located between power source and working element, power transmission is carried out through the air space. Absence of mechanical couplings leads to zero mechanical backlash of the linear drive.
Due to fewer stages of electrical power conversion into reciprocating movement, the linear drive ensures higher efficiency than the ball screw and rack & pinion.
Comparison of drive types
Wear
Unlike rack & pinion and ball screw coordinate systems, linear drives do not consist of mechanical components providing high reliability and low wear.
Backlash
System’s mechanical backlash affects directly the repeatable positioning accuracy. Due to higher number of mechanical joints coordinate systems based on ball screw unit and pinion rack have slightly larger backlash values.
Long travel precision
Regarding coordinate system based on linear drive, long travel precision is defined by feedback precision of position (magnet or optical scale), as well as precision of portal installation (right angle) and tracking system itself. Concerning coordinate systems based on ball screw and rack & pinion, the precision is defined by machine bed quality and quality of guides’ installation. Both cases require calibration of coordinate system using a laser interferometer. If production and engineering-technical facilities to provide the calibration are not satisfying, application of linear drive is preferable due to its simplicity.
Dynamics
Ball screw and rack & pinion coordinate systems have lower dynamic characteristics than the linear drive owing to design and technological features (a number of middle elements, backlash, sharp changes of tension in connected parts, screw pitch errors, etc.). Eventually all these factors will affect the machine dynamic characteristics.
Linear drive systems possess high dynamic characteristics during both movement trajectory control and positioning accuracy.
Reliability
Since the system based on the linear drive possesses smaller number of mechanical parts and joints it ensures the highest level of reliability. However, it is worth mentioning that a drive is not the only component of the laser cutting machine that affects the reliability, therefore, it is the general reliability of the system that shall be estimated.
Precision of travel along the contour hardly depends on the drive type, and it is defined by the rigidity of coordinate system structure (incl. portal), as well as by the frequency response of the coordinate system (which in its turn depends on structural features of the portal, head mounting and other components).
Precision of travel along the contour is also concerned with dynamic parameters of the coordinate system. Since the powerful drive is installed, the high dynamics at free running can be reached (with the switched off tool); if the machine construction is not rigid enough, the significant decrease of acceleration and deceleration values is required to provide the precision.
Pricing
The linear drive is more expensive than the ball screw or rack & pinion. The reason is that the direct drive requires long powerful neodymium “magnet way” along which the drive is moving. At the same time regular servo drive has smaller amount of magnets and they are located on the rotor, which rotates many times during working travel of coordinate.
The table can be scrolled left / right
Coordinate system based on the ball screw unit | Coordinate system based on the rack & pinion | Linear drive |
---|---|---|
Subject to wear. Heavy wear if low quality manufacturing. | Subject to wear. Heavy wear if low quality manufacturing. | No wearable components. |
Presence of carriage and drive backlash which affects the accuracy. | Presence of carriage and drive backlash which affects the accuracy. | Zero mechanical backlash. |
Reduced precision at long travels. | Reduced precision at long travels. | High precision at any travels. |
Average dynamics. | High traveling dynamics (if applying high performance drive). | High dynamics (if applying high performance drive). |
High reliability while maintaining proper quality of manufacturing. | High reliability while maintaining proper quality of manufacturing. | High reliability. |
Average cost. | Average cost. | High cost. |
In conclusion
The linear drive has some undeniable advantages. It leads to longer service life of equipment, increases accuracy and travel dynamics of coordinate system.
However, it cannot be claimed that ball screw and rack & pinion machines are obsolete. With the proper quality of manufacturing, they provide perfect solutions for entry-level machinery – low power machines with poor demand to speed and efficient production. Nevertheless, for more efficient machinery, the linear drive still ensures the highest dynamics and positioning accuracy.
Manufacturing the machines based on ball screw, rack & pinion and linear drive enables Unimach to offer our customers the best solutions considering cost, performance and reliability of every task.